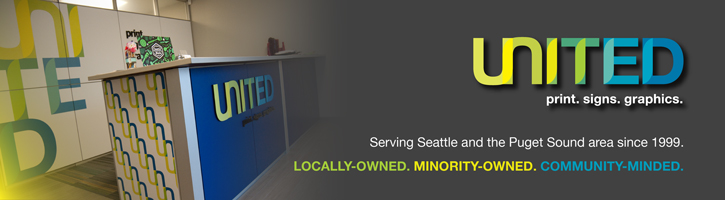
At United, our most valuable assets are our people. We employ and retain the most experienced printing professionals for all our key staff positions. Machines cannot perform the type of quality control that is necessary to ensure the level of service that we are committed to delivering. Our disciplined QC procedures extend throughout every department with built-in redundancy.
When a job is placed into production, the incoming QC department reviews the job for anomalies, checks the instructions to make sure all information is included, and they ensure that the files or documents match the work order.
When requested, our account representatives review hard copy proofs with the customer to check for accuracy, verify versions of print files and address any areas of concern before moving into production. This step can add on an extra day (or more) to turnaround times, but provides peace of mind on complicated and/or first-time print jobs. If not requested, customers have the option to review proofs online, via email or to run as-is.
Once in production, the operator reads the work order twice for accuracy. The files or documents are reviewed again to make sure they match the instructions. If a table of contents is provided, the files are matched against it to ensure the document is complete and that the pages display as expected.
A test run is performed to check the printing quality; spot checks are performed frequently during the run. The last print is then checked with the same attention to detail given to the initial test print.
A member of the outgoing QC department then reviews the job to check again that the quality level meets company standards. The instructions are reviewed again to ensure the job was output as ordered and then the documents are packaged for delivery.
The dispatch department then checks that the correct number of packages are assembled and that the documents are prepared in accordance with the client’s request. The delivery instructions are reviewed and the job is then loaded for the driver, who performs the final check. The driver reviews the delivery and packaging instructions one last time to make sure that the job is being delivered as requested.
Every member of every department understands the importance of consistently reviewing each printing job for accuracy.